La adaptación de la actividad productiva a los más modernos estándares de la organización industrial es hoy un importante valor agregado de las empresas, y en este sentido FAdeA, con su programa de Mejora Continua iniciado en marzo de 2014, es pionera a nivel nacional y se proyecta a nivel internacional. Para fines de 2015 se prevé que sean más de 20 los círculos de Mejora Continua implementados y que esta modalidad se extienda a otros actores que integran la cadena productiva de FAdeA.
Esa mejora continua no solamente implica estar actualizados tecnológicamente sino, sobre todo, adquirir una nueva filosofía de trabajo: “Desde marzo de 2014, FAdeA implementa un programa de Mejora Continua con la formación de círculos Kaizen, donde los propios trabajadores analizan los problemas que tienen en sus puestos de trabajo, los procesos con los cuales trabajan, y buscan soluciones concretas para minimizar el desperdicio de tiempo y de materiales”, explica Matías Savoca, presidente del Directorio de FAdeA.
En estos círculos Kaizen –término de origen japonés que significa “mejora continua hacia la calidad total”– el conocimiento necesario para organizar la producción no se concentra en los niveles directivos para ir “hacia abajo”, sino que “desde abajo” y desde los niveles medios surgen las prácticas que luego se convierten en estándar.
A lo largo de 2014 se logró implementar en la planta 11 círculos Kaizen en el marco del programa a cargo del Ing. Federico Presman. En ellos, los integrantes del propio equipo evalúan cómo solucionar cada problema planteado en el trabajo, proponen la mejora, la llevan a cabo y luego la estandarizan, es decir, la incorporan al método de trabajo.
Esta metodología es parte fundamental de lo que se conoce como Lean Manufacturing (o más popularmente, “toyotismo”, en oposición al “fordismo” que fue el modelo imperante en la industria en serie en todo el mundo durante el siglo pasado), entre cuyas características está la producción just-in-time: continua, a demanda y minimizando los stocks, lo cual requiere mucha más eficiencia en los procesos.
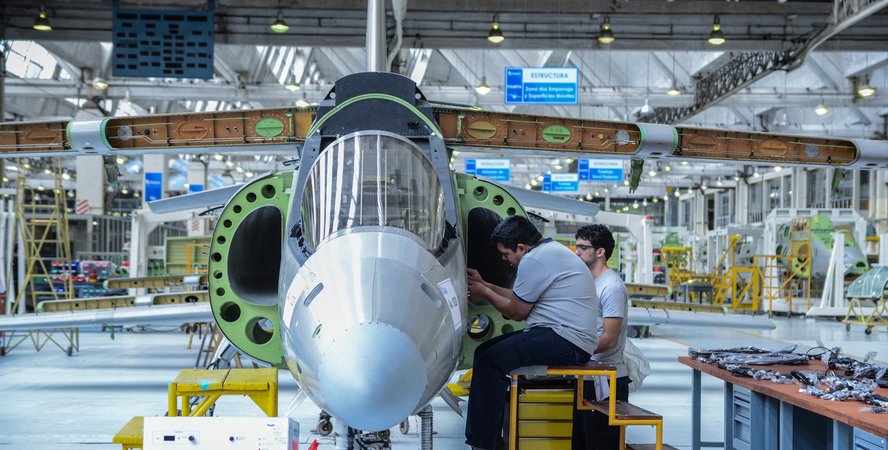
La línea de montaje en serie del avión de entrenamiento avanzado IA-63 Pampa III se ubica en el enorme Hangar 90 de FAdeA. En cada puesto de esa línea hay una unidad en su correspondiente etapa del proceso, de modo que a lo largo de las sucesivas etapas se puede apreciar, de principio a fin, la secuencia de fabricación como en una serie de fotogramas.
Las tareas en cada puesto vinieron prefijadas desde el diseño previo del proceso, naturalmente en busca de la optimización como objetivo.
El programa de Mejora Continua busca el compromiso de los trabajadores en la mejora de esos procesos. Los técnicos y operarios del equipo de Armado de Cabina del Pampa III implementaron un nuevo sistema de trabajo con el que lograron reducir un 23,7% el tiempo dedicado a cada estructura de cabina, superando incluso el objetivo inicial que era mejorarlo en un 20%. Lo hicieron mediante la implementación de un sistema pokayoke (palabra que en japonés significa “a prueba de errores”) con el que sistematizaron el ordenamiento visual de las piezas abastecidas a la línea de montaje, mediante una matriz que presenta los elementos de cada subconjunto de forma cómoda tanto para facilitar el proceso de armado como para comprobar inmediatamente que se encuentren todas las piezas necesarias, y que todas correspondan al subconjunto que se está ensamblando.
Esta medida relativamente simple permitió controlar dos de los que, según se analizó, eran los principales factores de desperdicio de tiempo en el armado de la cabina del Pampa: no advertir a tiempo la existencia de faltantes, y recibir piezas equivocadas o repetidas cuyo reemplazo hay que gestionar, con todos los retrasos que ello ocasiona.
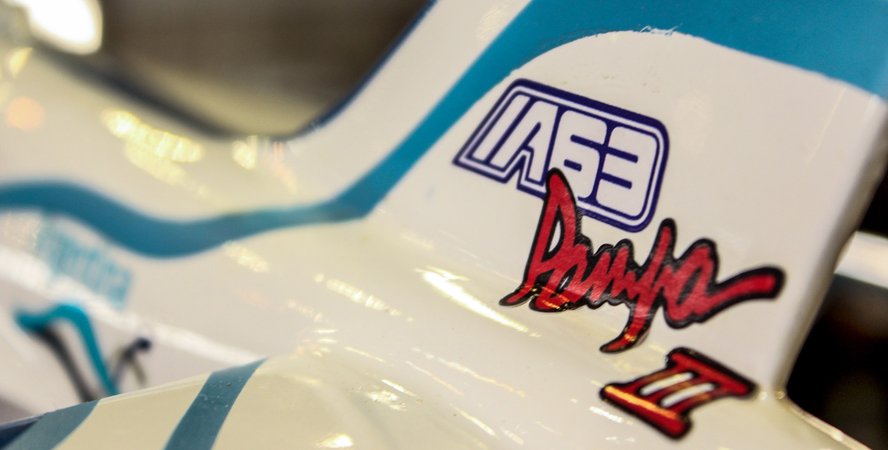
Las matrices pokayoke, diseñadas por quienes serían luego sus propios usuarios, sirven para disponer las piezas secuencialmente según el orden en que van a ser utilizadas, y a su vez fueron instaladas en las proximidades del subconjunto al que corresponde cada una. Este equipo Kaizen de Armado de Cabina del Pampa III fue distinguido por su tarea en la Convención Interna de FAdeA como el mejor grupo de año 2014, y planean exponer los resultados de su trabajo en el 20° Encuentro Nacional de Mejora Continua en setiembre en Buenos Aires en la sede del Instituto nacional de Tecnología Industrial (INTI), invitados por la Sociedad Argentina de Mejoramiento Continuo (SAMECO).
El programa de Mejora Continua de FAdeA también incluye la adaptación de las áreas de trabajo al estándar de calidad conocido como “5 S” y la incorporación de herramientas de gestión visual.
Las “5 S” surgen de los términos japoneses Shitsuke, Seiketsu, Seiso, Seiton y Seri, que resumidos significan desechar todo lo que no te sirve, ordenar lo que normalmente se utiliza en función de cómo se usa, una limpieza entendida “preventivamente” (no ensuciar, implementar medidas higiénicas que eviten, por ejemplo, que se tire cualquier residuo al suelo), la estandarización de todas las medidas implementadas con la respectiva demarcación del espacio para facilitarlas (por ejemplo, marcar en el piso el sitio donde va la mesa) y, por último, mantener la autodisciplina de transformar esta forma de trabajar en hábito. El método incluye establecer sistemas de medición estándar para cada una de las acciones que se realizan, porque el lema es que “lo que no se ha medido, no se puede resolver”.
La gestión visual, por otra parte, establece que cada área cuente con un “tablero de mando” con la información estratégica actualizada para la comunicación “hacia afuera” (con los niveles gerenciales) y “hacia adentro”. Con sólo mirar este tablero de un área, se puede saber qué se está produciendo allí, en qué estado de progreso se encuentra, cuál es la dinámica y, en caso de que haya algún eventual retraso, cuáles son los motivos. Así el líder del equipo está al tanto del 100% de lo que pasa en su taller y de las cuestiones que debe resolver, y mejora el canal de comunicación entre las diferentes áreas.
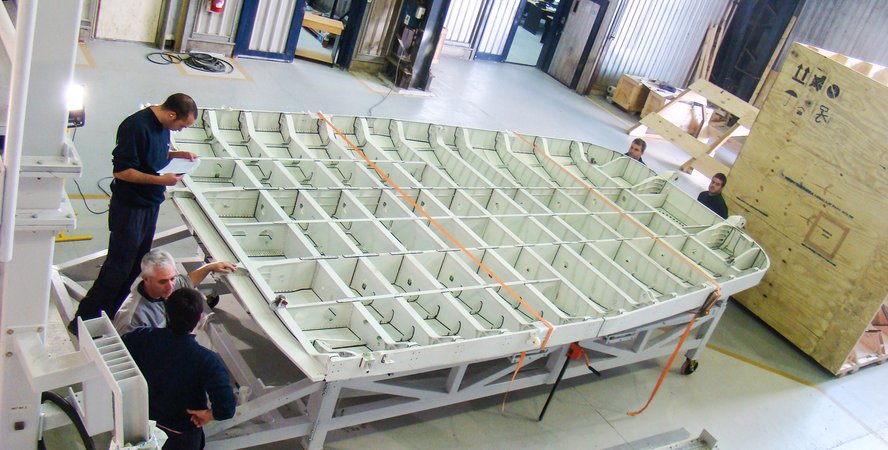
Hoy la Lean Manufacturing es el estándar de oro de la industria aeronáutica internacional, en la que FAdeA se ha insertado definitivamente gracias a la producción en serie y exportación de conjuntos para el avión carguero militar Embraer KC-390. Justamente, el Programa puso el acento en las áreas de trabajo con las partes del KC-390 y cuenta con el apoyo de la aeronáutica brasileña Embraer, que ha enviado a la Argentina a sus Kaizen Project Officers para capacitar y trabajar conjuntamente con el equipo local.